Design for Additive Manufacturing
Maximize your design and engineering potential with NX’s cutting-edge toolkit of additive design capabilities. Additive manufacturing is changing the way products are designed as well as how they are manufactured. Additive manufacturing greatly expands the possibilities for product design, allowing for topology optimized parts, lattice structures, meshing and geometric patterns. See more about these below.

Proven design tools for additively manufactured parts
Generating the desired output from the additive manufacturing process begins with the right design. Design for AM is more than just optimizing geometry, but also verifying the design will print as expected. Get the tools you need to ensure first-article print quality.
Unparalleled design tools
Leverage a complete parametric computer-aided design (CAD) system that enables you to work with non-uniform rational basis spline (NURBS), facet/mesh, and even sub-division bodies interchangeably and together in the same part. The robust design solutions available in NX mean you have all the tools necessary to design the simplest or the most complex printed parts.
Lattice Structures Design
A lattice structure is an architecture formed by an array of spatial arrangement of unit cells with edges and faces. These are cellular solids available in both two and three dimensions. With additive manufacturing, lattices bring many advantages. They reduce the mass of an object which means less material is used.

Implicit modelling
Implicit modelling allows you to create complex structures. The design of a complex geometric object can be divided into a set of simple shape-designing tasks, owing to the availability of shape-preserving implicit blending operations. It allows fast and automated formations of surfaces such as grade, faults and alteration directly from geological data.
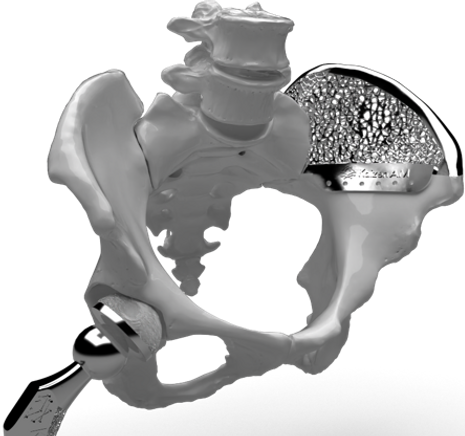
Algorithmic modelling
Algorithmic modelling provides designers with a drag-and-drop, no-code capability for creating reusable geometric patterned elements. Leveraging within the NX environment, algorithmic modelling lets users define the intent and rules for their design by connecting together inputs and outputs in a highly intuitive visual logic workflow.


Generative Engineering
Generative design is a design exploration process. Designers or engineers input design goals into the software, along with parameters such as performance or spatial requirements, materials, manufacturing methods, and cost constraints.
It allows for a combination of traditional technologies, such as feature modelling, and combines them with new technologies like design optimization and convergent modelling.

Topology optimisation
Topology optimization is an optimization method that employs mathematical tools to optimize the material layout within a given design space, for a given set of loads, boundary conditions and constraints with the goal of maximizing the performance of the system.
NX Nastran solver
-
Integrated into Simcenter 3D
-
Wide selection of FE modelling tools
-
Full suite of advanced FE post processing
Multiphysics
-
Linear Static
-
Normal Modes
-
Direct / Modal Frequency
-
Combinations
-
Simcenter Motion Loads

NX Features of Interest
Fluid flow optimisation
Capitalise on the strong fluid flow analysis capabilities in Star-CCM+ product as you apply that technology to topology optimisation. The result is a system that can optimize part geometry for efficient fluid flow, meaning you can optimize fluid systems to normalize flow between multiple outlets and direct the flow through a duct system in the most efficient manner.

Performance simulation
Simulate the performance of a printed design in real-world conditions once the design is complete. Simcenter 3D allows you to expedite the simulation process by combining best-in-class geometry editing, associative simulation modeling and multi-discipline solutions embedded with industry expertise.

Production readiness validation
Manage the unique requirements in additive manufacturing processes, including allowable overhang, print resolution and print volume. NX includes a series of integrated solutions for validating designs against these process requirements, allowing both the designer and the shop floor operator to be confident the designs released to manufacturing are printable. This saves time and money.
.jpeg)